YN-A501 Polymer (EVA/HDPE) Waterproof Sheet
Product Introduction
The YN-A501 Polymer (EVA/HDPE) Waterproof Sheet is made from polymer EVA/HDPE (ethylene copolymer/high-density polyethylene) and is produced by extrusion. It is used as a waterproof sheet for various engineering applications, including waterproofing, seepage prevention, moisture-proofing, gas-proofing, pollution prevention, and drainage.
The raw materials typically include: Ethylene Vinyl Acetate (EVA), High-Density Polyethylene (HDPE), and Ethylene Copolymer Bitumen (ECB) resin.
Product Features
-
High tensile strength, exceeding 16Mpa at room temperature; large elongation at break, exceeding 550% at room temperature; good stress resistance and crack resistance, easily adapting to water expansion and cracking of structures;
-
Excellent low-temperature bending performance, maintaining good flexibility even below -35°C; well-suited to changes in ambient temperature;
-
The product boasts excellent flexibility, wear resistance, puncture resistance, stable product dimensions, good adhesion, and ease of installation;
-
Resistant to corrosion from acids, alkalis, salts, and other media, as well as mold. It exhibits stable performance against acids, bases, and other chemicals in concrete or sandy soil, making it suitable for underground projects such as tunnels and civil engineering;
-
Excellent workability: the overlapping seams of the roll can be hot-melt welded to achieve the desired construction effect.
Specification and Model
Thickness: 1.0mm/1.2mm/1.5mm/2.0mm
Width: 1.0m/2.0m/3.0m
Length: 20m
Construction Method
The construction methods of waterproof sheets can generally be divided into three types:
① Anchor nail fixation method (hot-melt pad anchoring and welding);
② Laying method without anchor nails;
③ Concealed buckle tying and hanging method (strap suspension method).
The appropriate construction method can bebased on the product's structural form, construction site environment, and requirements.
(1) Requirements for base surface treatment: The base surface should be flat, clean, free of looseness, hollowing, and cracks, with a flatness that meets D/L=1/10.
D - The depth of the indentation between adjacent surfaces of the initial support base;
L - The distance between adjacent convex surfaces of the initial support base.
(2) Metal components protruding from the base, such as steel bar ends and anchor rod heads, should be cut off and smoothed with mortar. For metal components that cannot be cut off, such as anchor cable heads, they must be covered with sprayed concrete or mortar, with an arc radius R greater than 200mm.
(3) The internal and external corners and edges of the base surface need to be rounded with mortar, with an arc radius of 100mm.
(4) Only a small amount of occasional moisture stains are allowed on the base surface, and there must be no dripping, leaking, flowing, streaming, or sediment discharge. Before laying, carefully clean all debris from the base surface.
(5) When testing the double welds welded by a double-weld automatic welding machine, clamp the ends of the welds tightly with iron clamps to prevent air leakage. Then, insert a test needle into the air groove between the two welds and pressurize it with a manual air pump to 0.25Mpa. Observe for 15 minutes. If the pressure drop is less than 10%, it is considered qualified. If the pressure drop is too large and does not meet the requirements, promptly locate the leak and repair it.
Scope of Application
- Primarily used for waterproofing of tunnels in railways and subways;
- Engineering waterproofing for highway and railway culverts;
- Waterproofing, seepage prevention, and moisture-proofing projects for various municipal engineering, sewage treatment tanks, civil defense projects, and other construction projects;
- Seepage prevention projects for water conservancy, dams, drainage ditches, artificial lakes, and other projects.
Precautions
- When laying the plastic waterproof sheet, it should not be stretched too tightly, and sufficient allowance should be left based on the flatness of the base surface;
- The surface of the material at the welding points must be wiped clean and free from water, oil, and dirt;
- Strictly focus on inspecting the welding quality to ensure no missed welds or skipped welds.
Packaging, Transportation, and Storage
- The plastic sheet is rolled into a cylindrical shape and packaged with plastic bags or woven bags on the outside;
- During transportation and storage, care should be taken not to damage the packaging, and the materials should be placed in a ventilated, dry location;
- The stacking height for storage should not exceed the height of five flatly placed sheet rolls. When stacking, the materials should be placed on a dry, level surface, avoiding direct sunlight, and prohibited from contact with acids, alkalis, oils, organic solvents, etc. They should also be isolated from heat sources;
- During transportation, prevent tilting or squeezing, and cover with felt cloth if necessary;
- Under normal transportation and storage conditions, the storage period is 1 year.
Technical Indicators
Meet the relevant standards for resin homogeneous sheets and composite sheets in GB18173.1-2012.
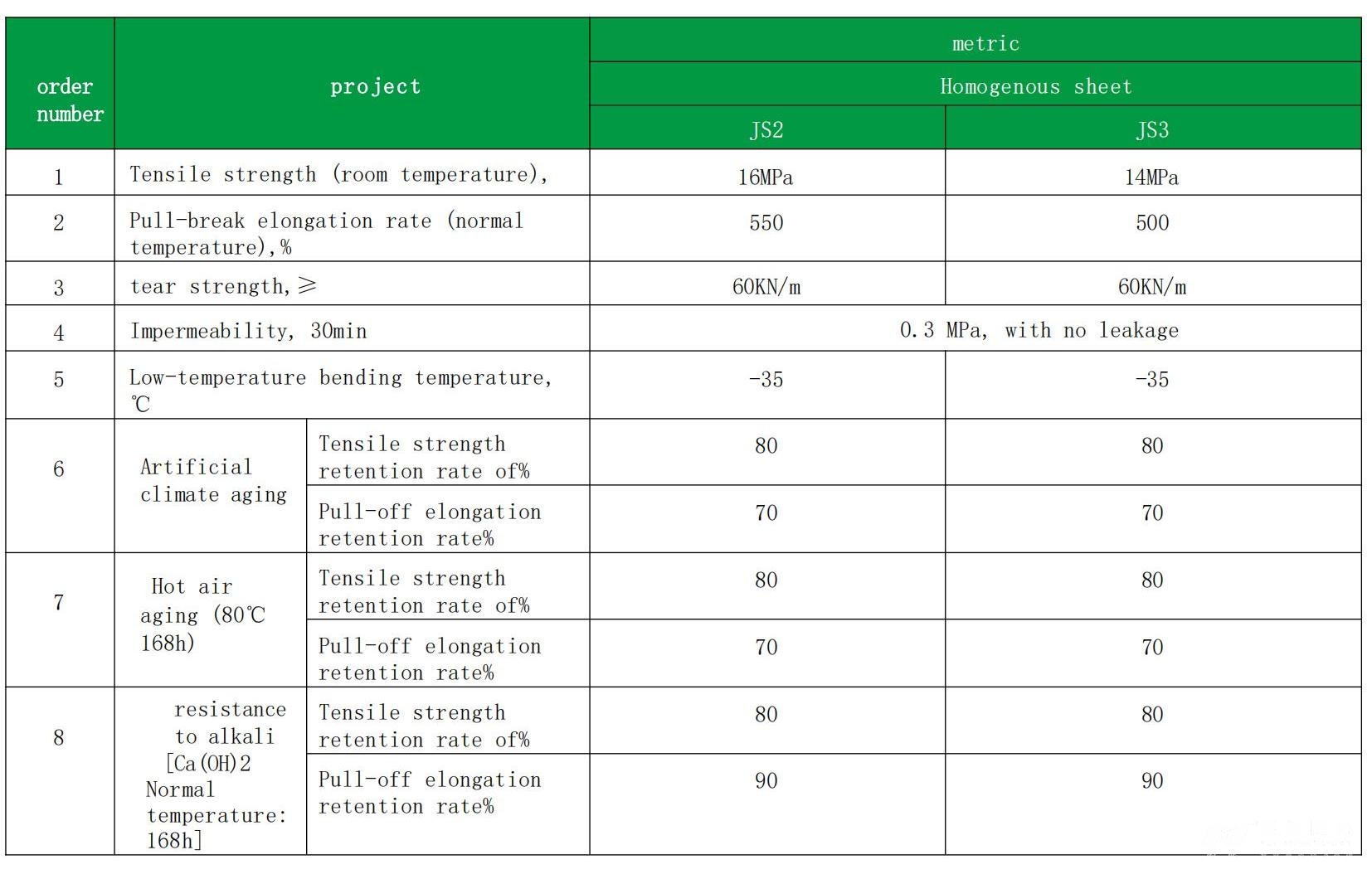